在方管拉弯过程中,裂纹的产生是一个需要高度重视的问题。为了避免裂纹的产生,需要从材料选择、工艺控制、模具设计、后期处理等多个方面入手,确保拉弯过程的顺利进行和产品质量的稳定。以下是一些具体的措施和建议:
一、材料选择与预处理
选择高质量材料:确保所选方管材料内部组织均匀,无夹杂物、气孔、裂纹等缺陷。材料的化学成分和力学性能应符合相关标准,以保证其具有良好的可塑性和韧性。
预处理:在拉弯前,对方管的表面进行清洁处理,去除油污、灰尘等杂质,以提高材料的表面质量和附着力。对某些特殊用途的方管,如需要提高耐腐蚀性的,可进行适当的表面处理,如氧化、喷涂等。
选择高质量材料:确保所选方管材料内部组织均匀,无夹杂物、气孔、裂纹等缺陷。材料的化学成分和力学性能应符合相关标准,以保证其具有良好的可塑性和韧性。
预处理:在拉弯前,对方管的表面进行清洁处理,去除油污、灰尘等杂质,以提高材料的表面质量和附着力。对某些特殊用途的方管,如需要提高耐腐蚀性的,可进行适当的表面处理,如氧化、喷涂等。
二、工艺控制
控制拉伸力和速度:根据方管的材质和截面尺寸,计算并控制拉伸力的大小,避免拉伸力过大导致材料受损或产生裂纹。保持稳定的拉伸速度,确保材料能够均匀、平稳地变形,避免速度过快或过慢导致的应力集中。
优化弯曲角度和曲率:根据方管的材质和截面形状,合理设计弯曲角度和曲率半径,以减少弯曲过程中的应力集中和截面畸变。弯曲角度不宜过大,曲率半径应适当,以确保材料在弯曲过程中能够均匀受力。
控制拉伸力和速度:根据方管的材质和截面尺寸,计算并控制拉伸力的大小,避免拉伸力过大导致材料受损或产生裂纹。保持稳定的拉伸速度,确保材料能够均匀、平稳地变形,避免速度过快或过慢导致的应力集中。
优化弯曲角度和曲率:根据方管的材质和截面形状,合理设计弯曲角度和曲率半径,以减少弯曲过程中的应力集中和截面畸变。弯曲角度不宜过大,曲率半径应适当,以确保材料在弯曲过程中能够均匀受力。
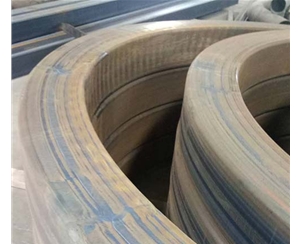
三、模具设计
调整模具间隙:根据方管的截面尺寸和材质特性,适当调整模具的间隙,以确保材料在弯曲过程中不会因为间隙不当而受到过大的挤压或拉伸力。模具间隙应均匀,避免局部应力集中。
模具材料选择:选择具有高硬度、高耐磨性和良好韧性的模具材料,以提高模具的使用寿命和减少因模具磨损而产生的裂纹风险。模具的表面应光滑,以减少对方管的摩擦和损伤。
调整模具间隙:根据方管的截面尺寸和材质特性,适当调整模具的间隙,以确保材料在弯曲过程中不会因为间隙不当而受到过大的挤压或拉伸力。模具间隙应均匀,避免局部应力集中。
模具材料选择:选择具有高硬度、高耐磨性和良好韧性的模具材料,以提高模具的使用寿命和减少因模具磨损而产生的裂纹风险。模具的表面应光滑,以减少对方管的摩擦和损伤。
四、后期处理与校正
热处理:对拉弯后的方管进行适当的热处理,如退火或淬火,以消除内部应力和改善材料的机械性能。热处理温度和时间应根据材料的种类和厚度进行合理选择。
校正处理:对拉弯过程中产生的微量变形或偏差进行后期校正处理,以确保产品的尺寸精度和形状符合要求。校正方法可根据实际情况选择机械校正或热处理校正等。
热处理:对拉弯后的方管进行适当的热处理,如退火或淬火,以消除内部应力和改善材料的机械性能。热处理温度和时间应根据材料的种类和厚度进行合理选择。
校正处理:对拉弯过程中产生的微量变形或偏差进行后期校正处理,以确保产品的尺寸精度和形状符合要求。校正方法可根据实际情况选择机械校正或热处理校正等。
五、质量检测与监控
在线检测:在拉弯过程中设置在线检测装置,实时监测方管的变形情况和表面质量。及时发现并处理潜在的问题,如裂纹、变形等。
成品检验:对拉弯后的成品进行严格的检验和测试,包括尺寸测量、表面质量检查、力学性能测试等。确保产品质量符合相关标准和要求。
在线检测:在拉弯过程中设置在线检测装置,实时监测方管的变形情况和表面质量。及时发现并处理潜在的问题,如裂纹、变形等。
成品检验:对拉弯后的成品进行严格的检验和测试,包括尺寸测量、表面质量检查、力学性能测试等。确保产品质量符合相关标准和要求。
综上所述,通过选择高质量材料控制工艺参数、合理设计模具、后期处理与校正以及质量检测和监控等措施,可以有效地避免方管在拉弯过程中产生裂纹。这些措施的实施将有助于提高产品的质量和生产效率,降低生产成本和风险。